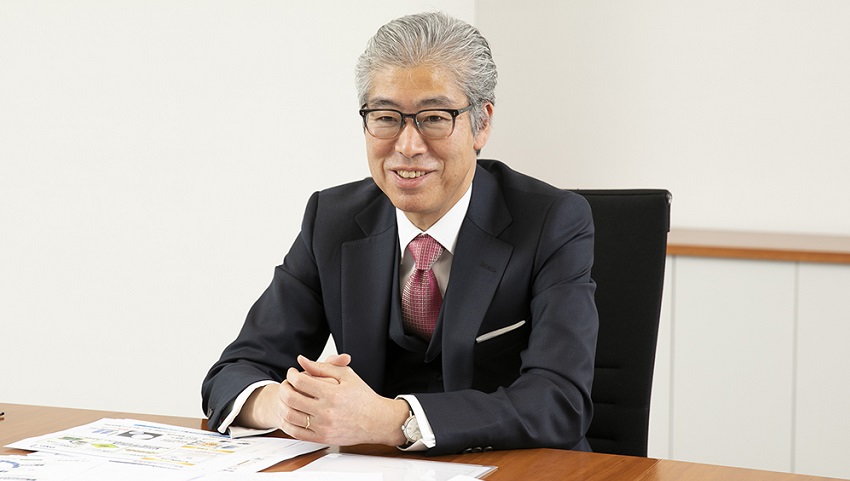
カーボンニュートラル実現に向けたDNPの環境配慮技術
- X(旧Twitter)にポスト(別ウインドウで開く)
- メール
- URLをコピー
- 印刷
2020年10月に政府が宣言した「2050年のカーボンニュートラル」に先駆け、DNPは同年3月に「DNPグループ環境ビジョン2050」を策定し、持続可能なより良い未来に向けた「脱炭素社会」「循環型社会」「自然共生社会」の実現への取り組みを加速させています。このビジョンを推進し、具体的な製品・サービスを生み出す大きな強みとなっているのが、モノづくりの現場で培ってきた技術力です。今回、研究開発・事業化推進センター 基盤技術開発本部を率いる楠川宏之(くすかわ ひろゆき)が、DNPの環境配慮技術や環境配慮製品・サービスの一端についてご紹介します。
目次
- サプライチェーン全体でサステナビリティを考える時代
- 環境配慮材料の活用事例——必要な材料を組み合わせて実現する「バイオマスプラスチック」の多機能化
- 半導体・情報通信産業分野の開発事例——電力消費を抑える「高密度実装」ほか
- 自動車・蓄電池産業分野の開発事例——急速充電と高出力を実現する「全固体電池用包材」ほか
- 技術の力で未来をつくり出す、DNPの挑戦
サプライチェーン全体でサステナビリティを考える時代
研究開発・事業化推進センター 基盤技術開発本部:本部長 楠川宏之 |
DNPのモノづくりの現場では常に、「新しい価値を提供するためにどうするかという視点」で技術研究開発を進めています。近年はこれに加え、「サステナビリティ(持続可能性)に貢献する視点」が欠かせません。
カーボンニュ―トラルの実現に向けて、環境負荷の低い持続可能な製品・サービスが社会全体で求められている中、DNPはサプライチェーン全体を通して環境負荷低減に貢献する製品・サービスの開発、並びにそれを支える技術革新に取り組んでいます。
特に「モノづくり」については、人々の暮らしのなかでの利用シーンも視野に入れて、「持続可能な原材料の調達」「原材料使用量の削減」「使用時の環境負荷低減」「長期使用」「リサイクル・リユース」という5つの方針(図1)を掲げ、グループ全体でさまざまな施策を推進しています。
図1:サプライチェーン全体を視野に入れたDNPの環境負荷軽減の取り組み
|
中でも特に成果を挙げつつあるのが、石油由来ではなく植物由来の原料を使うことで環境負荷を低減するバイオマス材の活用を中心とした「環境配慮材料の活用」と、政府のグリーン成長戦略でも重視されている「半導体・情報通信産業分野」、電気自動車(EV:Electric Vehicle)用や家庭用・産業用蓄電池としても期待される「自動車・蓄電池産業分野」での技術研究開発です。これらの最新実績をご紹介します。
環境配慮材料の活用事例——必要な材料を組み合わせて実現する「バイオマスプラスチック」の多機能化
サプライチェーン全体に深く関わる「材料」の分野でDNPは、さまざまな環境配慮材料の開発・製造に力を入れています。温室効果ガスの排出量の削減には、従来の石油由来のプラスチックではなく植物由来の原料を使用したバイオマスプラスチックを用いることが有効です。
DNPは2006年に、植物由来の原料を使用したバイオマスプラスチックのパッケージを開発し、2011年にはサトウキビ由来の原料を使用した「DNP植物由来包材 バイオマテック®」(図2)を開発して、実用化を進めてきました。
開発にあたっては、生態系や環境に与える影響を定量的に評価するLCA(ライフ・サイクル・アセスメント)に基づいて、生産国のサトウキビ農園において現地調査を実施。併せて植物を原料としていることから水資源の消費による影響も調査しています。
完成した「DNP植物由来包材 バイオマテック®」は石油由来プラスチックと物性が変わらず、これまでのパッケージと置き換えるだけで環境に配慮することができ、現在、さまざまな内容物に適用し、用途を広げることに成功しています。
図2:「DNP植物由来包材 バイオマテック®」のライフサイクル
|
サトウキビから砂糖を精製した際の副産物(廃糖蜜)を原料の一部に使用して、石油資源の使用量を削減。またサトウキビが育つときにCO₂を吸収するため、製品のライフサイクル全体でカーボンニュートラルに貢献します。 |
開発において重視したのは、植物由来の原材料でも、石油由来の原材料で作ったものと同等の機能を持った製品にすること。植物由来の原材料を使うとプラスチックとしての機能が限られるため、長年の研究開発で培ってきたコンバーティング技術(※1)により、「機械的特性(シール強度、耐衝撃性など)」、「バリア性」などのパッケージに必要な機能を付与する必要がありました。
- ※1:コンバーティング技術=材料の形を変える・複合するなどの材料加工技術。製膜・コーティング・ラミネート・賦型・転写・切断・研磨・製袋・成型・製本など、紙やフィルム等の素材の加工技術を指す。
DNPは、食品や日用品等のパッケージから得た、カーボンニュートラル実現のニーズに応える豊富な知見を強みに、床材や壁面材等の生活空間用製品、エレクトロニクス製品まで、幅広い分野で環境配慮材料を展開しています。
例えば、自動車のサンルーフやドアの上のサイドバイザー、内装材などにも、必要な機能を付与したバイオマス製品を浸透させていきます。また、ICカードなど多くの製品で環境に配慮した開発を進め環境負荷の低減につなげていきます。
「環境に配慮した材料」であることは、今やあらゆる産業が求める必須条件といえます。単に「安い」「機能がいい」だけでは、もはや選ばれない時代です。そうしたニーズにいち早く対応し、さらに先取りできるよう、DNPはバイオマスプラスチックの開発・認知拡大に取り組んでいきます。
半導体・情報通信産業分野の開発事例——電力消費を抑える「高密度実装」ほか
DNPは印刷技術のひとつである微細加工技術を応用・発展させて半導体関連製品を製造しており、この分野でもカーボンニュートラル実現に向けた技術研究開発に取り組んでいます。
近年、AI(人工知能)や5G通信サービスの広がりにともない、データセンターの電力消費量が上昇を続けており、2030年には世界の消費電力の約1割をデータセンターが占めるという予測もあります。そこで求められているのが、半導体製品の「高性能化」と「電力消費量の低減」という本来なら相反する条件を両立する技術の開発です。
この課題に対してDNPは、国立研究開発法人新エネルギー・産業技術総合開発機構(NEDO)が支援する共同事業体の1社として、基板の配線を短くして電気抵抗を抑え、高性能かつ小型な半導体製品を実現する「高密度実装向け中継部材(インターポーザ)」(図3)の研究開発に取り組んでいます。
DNPは、その鍵となる、半導体チップを近距離で高密度に接続し、さらに配線劣化による抵抗上昇を抑えることで余分な電力を消費しないようにする「中継部材(インターポーザ)」の開発を担当しています。独自の配線保護膜を開発するなど、DNPのさまざまな技術が「高密度実装」に活きているのです。
図3:高密度実装向け中継部材(インターポーザ)の概要
CPU(中央演算処理装置)やメモリなど、機能が異なる複数の半導体チップを1つの基板上に高密度で実装し、処理速度を向上させるパッケージング技術。DNPが開発した「インターポーザ」は、複数の半導体チップと基板を電気的に接続(中継)する重要な役割を果たす。 |
また、半導体製品製造時の消費電力を抑えるため、微細なパターンをハンコのように圧着させて転写加工を施す製造技術「ナノインプリントリソグラフィ(※2)」の開発にも取り組んでいます。現在までに、関係各社とのシミュレーションにおいて、製造工程の消費電力を約10分の1に抑えることに成功しており、製品化の目処も立っています。
-
※2:「ナノインプリントリソグラフィ」の節電効果について詳しくはこちらをご覧ください。
Discover DNP 半導体製造のカーボンニュートラルを加速する「ナノインプリントリソグラフィ」
自動車・蓄電池産業分野の開発事例——急速充電と高出力を実現する「全固体電池用包材」ほか
半導体と同じくEV用バッテリーも、カーボンニュートラルの実現に向けた重要領域のひとつにあげられています。DNPは、1990年代後半にリチウムイオン電池用バッテリーパウチの実用化に成功しました。これは、プラスチックフィルムを多層化して多様な機能をもたせたもので、従来の金属缶より軽量かつ形状の自由度が高いという強みを有しています。
現在は、同製品を国内外の電池メーカーに提供して世界トップシェアを獲得しています。こうした実績に関連する要素技術を融合して、次世代のEV用バッテリーの開発に取り組んでいます。
リチウムイオン電池用バッテリーパウチ |
この分野で大きな課題となっているのが、EVの普及に欠かせない「急速充電」と「高出力」の実現です。電解液や有機溶剤を内包する構造の現在のバッテリーでは、短時間で大きなエネルギーを溜め込んだり、一気に放出したりすると、高温になって発火する恐れがあります。5G通信サービスで単位時間あたりのデータ量が増えるモバイル端末などでも同様のことが想定されるため、EVにとどまらない社会インフラ全般に関わる課題となっています。
この課題を解決するため、現在、DNPも参画する産官学連携の技術研究組合リチウムイオン電池材料評価研究センター(LIBTEC)が研究開発を進めているのが、「全固体電池(※3)」です。全固体電池は、引火性溶媒を使用しないため耐火性が高く、冷却等の仕組みを必要とせずに急速充電が可能で、従来以上の高出力にも対応できます。
-
※3:「全固体電池」の開発について詳しくはこちらをご覧ください。
Discover DNP ノーベル化学賞の吉野彰理事長に訊く【前編】環境問題をリチウムイオン電池が解決?!
図4:全固体電池の概要
正極・負極に引火性の溶媒ではなく、粉末状の固体電解質を使用することで、電池の安全性が大幅に向上。 |
DNPは、このプロジェクトで培った知見も活かしながら、独自の取り組みとして次世代電池向けの包材の開発や製造技術の研究を進めています。
技術の力で未来をつくり出す、DNPの挑戦
「2050年カーボンニュートラル」という目標に向けて、持続可能な社会の実現が喫緊の課題となっていますが、こうした“人や社会を起点に考える”視点は、DNPが創業以来掲げてきた理念と重なります。
「P&I」つまり印刷と情報(Printing & Information)の強みを応用・発展させ、情報コミュニケーションや生活・産業、エレクトロニクスの事業部門で、幅広い製品・サービスを提供してきた道のりには、常に社会課題を解決し、人々の期待に応えるという想いがありました。「DNPグループ環境ビジョン2050」も、この想いを再構築したものと言えます。
|
技術的な視点で見ると、そこに2つのアプローチが必要だと考えています。まず、その時代を生きる人には想像し得ない新たな領域を切り開く「開拓」のアプローチであり、もうひとつは、切り拓いた領域で具体的な製品・サービスを生み出す「深化」のアプローチです。
これまで話したコンバーティングや材料開発、電子モジュール製造や微細加工などの多様な技術も、印刷工程の加工技術から発展させてきたものです。技術を強みとして、広範な事業領域を形作るに至った原動力は、この「開拓」と「深化」の反復による技術革新にほかなりません。「開拓」は、社内連携のハブである本社の開発部門が主体となり、「深化」は、顧客企業やマーケットとの接点を持ち、そこからの課題を認識している各事業部が主体となって、それぞれの立場から連携してきた歩みとも言えるでしょう。
2030年の達成をめざすSDGsでは、「気候変動に具体的な対策を」「つくる責任つかう責任」などのゴールが掲げられています。また、2022年の現時点では、「脱炭素社会」や「製造業CPS(サイバー空間と物理空間の相互作用を前提とした製造システム)」といったキーワードが衆目を集め、製造業の“常識”も大きく変わろうとしています。
そうした状況を踏まえ、技術の価値、技術への期待はこれまで以上に高まっていると実感しています。「オールDNP」の総合力の中で“人や社会に根ざした技術力”を強みとして、新しくより良い未来の創出に向けた挑戦をさらに推し進めていきたいと考えています。
![]() |
---|
大日本印刷株式会社
研究開発・事業化推進センター 基盤技術開発本部 本部長
楠川宏之(くすかわ ひろゆき)
1985年大日本印刷株式会社入社。ミクロ製品研究所にて液晶ディスプレイ用カラーフィルターの開発に従事。その後、プラズマディスプレイパネル用背面板、タッチパネル基板など主にディスプレイ用部品に関する研究開発を担当。2011年から研究開発センターにて中長期の新製品開発を担当。「次世代プリンテッドエレクトロニクス技術研究組合」理事、「技術研究組合単層CNT融合新材料研究開発機構」監事、「技術研究組合リチウムイオン電池材料評価研究センター」運営委員など、社外の技術研究組合での活動も経験。2021年10月から現職。
- ※掲載された情報は公開日現在のものです。あらかじめご了承ください。
- X(旧Twitter)にポスト(別ウインドウで開く)
- Linkdin
- メール
- URLをコピー
- 印刷